HORIZONTAL BALERS
Open End Auto-Tie and Closed End Manual-Tie Horizontal Balers
Makabale horizontal balers are recommended when vertical balers are too labor intensive and the waste volume is much too substantial than vertical balers can handle. Makabale offers you in its line both open end horizontal balers and closed end horizontal balers. They are also called as fully automatic horizontal balers and semi-automatic horizontal balers.
Be assured of user-friendly operation when you avail of the Makabale horizontal baler. The compaction cycle of these horizontal balers is automatic, as there are photoelectric sensors installed in the hopper to detect the material level and activate cycling, and they can be coordinated with bin tipper, infeed conveyor, air system, shredder and other choices, depending on your real site baling scenario.
CHOOSE WHICH BALER TYPE YOU ARE LOOKING FOR:
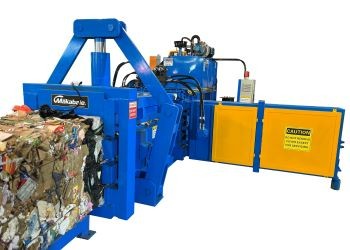
AUTO-TIE / AUTOMATIC HORIZONTAL BALER
- Bales multiple materials (cardboard, paper, soft plastic, etc.)
- Bale size: 720 x 800mm to 1100 x 1100mm
- Bale wt.: 200 to 1200kg (OCC)
- 6 different models and sizes
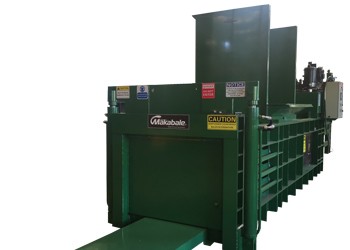
CLOSED END MANUAL TIE HORIZONTAL CARDBOARD BALER
- Bales multiple materials (cardboard, plastic, plastic bottle, textile, etc.)
- Bale size: 750 x 750mm to 1100 x 1250mm
- Bale wt.: 200 to 1350kg (OCC)
- 6 different models and sizes
What is a horizontal baler? As one of the main recycling baler types in the industry, a horizontal waste baler compresses the waste materials in a horizontal orientation with the material fed from the top of the machine. Once a bale is complete, it will be tied off and then pushed out from the side of the baler. The operator moves the bales away by forklift to where they are stacked and stored for shipping and recycling afterwards.
Usually, horizontal balers have a material loading hopper which can be designed into different shapes and sizes to adapt to different loading methods. Typically, a horizontal baler will be the preference of choice when the waste processing volume exceed 1 ton per hour.
Parts of a Horizontal Baler
A horizontal baler machine is mainly made up of below parts:
- Main body: where the waste material or recyclables are compressed and baled.
- Hopper: it is mounted on top of feeding mouth of the baling chamber. Hopper can be made into various shapes to adapt to different feed systems selected by users.
- Bales exit channel: it is part of the baling chamber where the compacted material is tied off and extruded out from the baler.
- Shrinking structure: it is the tension system on the bale exit chute, which generates tensioning force from all sides on the compressed material, while increasing the resistance to the advancement when the compaction cylinder is pressing the material to ensure high dense bales.
- Compaction trolley: it is the part used to compact the material. Just like the platen of vertical balers.
- Hydraulic compaction cylinder: it is connected to the compaction trolley and generate hydraulic power to complete material compressing cycle (forward compressing and retract)
- Hydraulic power unit: it consists of many components such as oil tank, pump, oil pipes, oil cooling system, hydraulic valves, pressure gauge, etc.
- Wire binding unit: including wire threading, wire cutting, and wire twisting units to complete the automatic tying system for an auto-tie baler.
- Electrical system: consists of many electrical parts such as PLC, relays, contactors, air breaker, buttons, travel switches, indicator, etc.
Horizontal Balers Are Usually Classified into Two Groups: Closed-door Baler (Closed-end Baler) and Open-end Baler.
Closed-Door Baler
A closed-door baler is a manual-tie baler and sometimes called semi-automatic horizontal cardboard baler. Waste materials are fed into the hopper by either conveyor, dumper, or hand, the machine compacts the materials automatically until a bale is made, then the operator needs to manually tie off the bale. The chamber door at the baler end will automatically open, and then the finished bale will be ejected out.
The closed-door baler is more productive than a vertical baler, but not as large as an automatic horizontal baler with the same pressing force. If your recyclable waste volume is more than a vertical baler can handle, a closed-door baler can be recommended.
Advantages of Closed-Door Baler
1. Higher capacity than vertical baler
2. Produce consistent mill sized bales. Bales usually bigger than that made by vertical balers.
3. Adapt to many types of feeding equipment. Saving labor cost.
4. Less space occupied than open-end automatic horizontal baler.
5. Less cost than open-end automatic horizontal baler.
Disadvantages of Closed-Door Baler
1. Bigger footprint than vertical baler.
2. Need manually tie the bale. So, it is not as efficient as an auto-tie baler.
3. Higher cost than vertical baler.
Open-End Baler
An open-end baler is typically with an automatic wire tying system and has an open end of the baling chamber. This horizontal cardboard baler is suitable for businesses who handle large volumes of materials, usually more than 15 tons (OCC) per day.
The open-end baler can also connect with different options of feeding equipment. Such as in-ground or above-ground conveyor, grapple, and air system. From the material feeding to completed bale comes out, the whole process is fully automatic. What you only do is to see the materials continuously loaded into the hopper and the uniform bales continuously ejected out from the bale exit.
Advantages of Open-End Horizontal Baler
1. Fully automatic baling process. Free up your staff’s time to do other work
2. High productivity and bigger bales produced by the machine.
3. Save labor and save time
4. Can process a wide variety of materials.
5. Easy to use and efficient
Disadvantages of Open-End Horizontal Baler
1. Higher cost than closed-end balers and vertical balers
2. Bigger footprint
What Materials Can Be Baled by Horizontal Balers?
Numerous materials can be baled with Makabale horizontal balers like PET bottles, cardboard, OCC, paper and soft plastic packaging. The output created are highly dense mill sized bales that are consistent and optimized for either container or truck shipping, and can be delivered directly to recycling plants for processing, creating more revenue stream for your business. Other than these common materials, our auto-tie balers can also bale plant fibers (such as coir fiber and alfalfa) and RDF.
Industries That Require Horizontal Balers
Our cost-effective horizontal balers are ideal for any places where large volumes of waste need to be processed as they have automatic feeding feature which is far more productive than manual feeding and they are far more effective to do baling work for businesses such as manufacturing plants, distribution centers, printing plants, recycling plants, warehouse, logistics centers and huge supermarkets.
How to Purchase the Right Horizontal Baler?
There are many horizontal balers and models in the market, either closed door baler or auto-tie baler. In Makabale, we have 5 standard models in closed door series with pressing force ranging from 40tons to 120tons, and 7 standard models in auto-tie baler series with pressing force ranging from 20tons to 120tons. When you are looking to purchase a new horizontal baler machine, there are a few things you need to consider which can help you determine which baler model to choose:
- Your baling material type. Each material has its own characteristics which will have different reaction in compaction process. For example, PET bottles are hollow and light plastic which has high rebounding force when pressing, so the closed-door baler would be a better choice than auto-tie baler because the bottles are compacted against the closed door of bale chamber which ensures dense and secure bales. While auto-tie baler is with open end chamber, PET bottle bales would be relatively less dense and secure than closed-door type.
- Your processing volume. Each baler model has different capacity. You processing volume mainly determines which model to choose. If your processing volume is about 1 to 4 tons per hour, you can choose from closed door manual tie horizontal baler series. While for volumes more than 4 tons per hour, the auto-tie baler is often the ideal choice. But if your volume is only 1 to 3tons, you still prefer a fully automatic baling system, we have small and compact auto-tie baler model options which are 20ton and 40ton models.
- The available space for installation and operating the machine. Horizontal balers usually take up more floor area. The size of small model and big model differs a lot. Check your available space and baler dimensions to make sure there is enough space for your baling project.
- Your budget. This is also an important aspect to consider when purchasing a new equipment.
Tips on Using Horizontal Balers
Horizontal baler machine can help your operation reduce large volumes of waste and make your recycling business more profitable and efficient. Automatic cardboard baler is easy to operate, but as a machine, using them correctly is vital to reduce the downtime and keep safety. Here are some tips for the horizontal balers.
- Make sure the doors of electric box and operation box are closed. This will avoid electric short circuit caused by moisture or dust.
- All pressure of hydraulic power unit is adjusted to optimal condition. Any adjustment should be under the permission of machine supervisor.
- If you cannot start the motor, it is highly possibly caused by thermal relay overload of the magnetic switch of motor. Check and find out the reason that causes overload, then reset the “Reset” bar.
- Always keep the horizontal cardboard baler clean and maintain the machine periodically according to maintenance guidance. Check and tighten all bolts and screws (especially at electric connection) to avoid abnormality.
- Always check the wires to make sure each wire is going through in order.
- If the ram moves forward and backward without stop, it may be due to some material residue stuck in front of the photo sensor inside the hopper. Simply remove the material residue to resolve the matter.
- If the machine encounters difficulties to complete the baling cycle, stop the motor and let the threaders move back to its home position. If threaders are not back to home position for more than one hour, it is likely damaged.
- Feed materials continuously and in uniform speed to maximize the throughput.
- Hydraulic oil should be changed 6 months after commencing operations. After that, change it once a year.
- Make sure temperature of hydraulic oil is within 0 to 60 degrees Celsius when the machine is in operation.
- Make sure the hydraulic station is in a ventilated area.
Choose from these two types of horizontal balers and select the model which meet your requirement. The machines can also be customized as per your particular baling needs. Contact us today to discuss your baling needs! we can help you determine which model best suits your operation.
Got a Question About The HORIZONTAL BALERS?
Talk with One of Our Experts in Waste Recycling Solutions
Our skilled professional team is waiting to help you with your unneeded waste materials and propose to you our recycling solutions. We also back up these proposals with our able technical support to make your recycling efforts earn more money by being more efficient.