Why Recycle PET Bottles?
PET bottle is one of the most widely used packaging material for carbonated drinks, beverage, water, juice, and tea owing to its nature of highly recyclable and many advantages. Recycle the post-consumer PET bottles is very crucial because there are a lot of benefits either to environment or the economics. For example:
- Reducing plastic pollution of the ocean. Plastic garbage is a major environmental problem for the oceans, which are home to over 50% of the Earth's species. Marine animals consume plastics that harm their digestive systems and can lead them to starve or die from lack of nutrients.
- Reduced greenhouse gas (GHG) emissions. Recycling PET bottles helps reduce GHG emissions because of the energy used to make new bottles.
- Save natural resources. Plastic bottles are made from petroleum and natural gas, which are non-renewable resources. Using recycled PET bottles helps save precious natural resources.
The recycled PET pellets can be remolded into new products such as water bottle, plastic bag, food tray and many more.
While its hollow characteristics makes the plastic bottles difficult and costly in disposal and transportation. Therefore, during the PET bottle recycling processes, one of the most important steps is to flatten and compress them into square dense bales by using PET bottle balers, which is a type of hydraulic recycling baler to reduce the waste size.
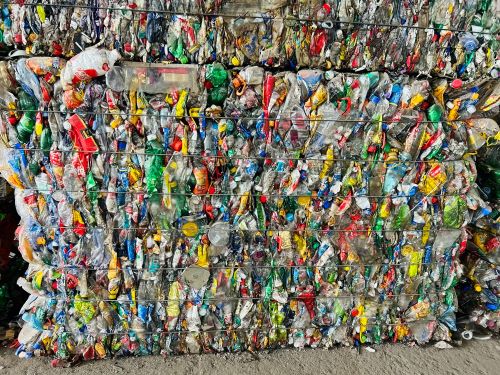